The swimming pool sand filter mainly uses quartz sand as the filter medium. It can be divided into three types: Glass fiber tank sand filter, 304 stainless steel tank sand filter, and 316L stainless steel tank sand filter. The shelf life and service life of the materials differ. Stainless steel materials offer high temperature resistance, corrosion resistance, long life, good sealing, high precision, high efficiency, and thorough backwashing. This paper mainly introduces the types, filtration process, and filtration speed of pool sand filters.
Filtration process of pool sand filter
Step 1:A certain scale of quartz sand or activated carbon and other filter media is generally placed in the pool sand filter. In a certain range, the size of the quartz sand is different, and it is arranged in the sand tank from top to bottom, from small to large.
Step 2: In normal filtration, water enters from the upper layer of sand and comes out from the lower layer. As the water flows through the filter layer from the top, some of the solid suspended substances enter the small empty holes formed by the upper filter material, getting absorbed and trapped by the surface layer of the filter material in a mechanical retention effect.
Step 3: At the same time, there is overlap and bridging between these suspended substances, as if a thin film is formed on the surface of the filter layer, which is called the filter cake, thereby enhancing the ability to filter the suspended substances. This is the so-called membrane filtration of the surface layer of the filter material.
Step 4: This filtration is not only the surface of the filter layer, when the water enters the intermediate filter layer also has this interception effect, in order to distinguish from the surface layer of filtration, this effect is called osmotic filtration.
Step 5: In addition, because the sand particles are closely arranged with each other, when the suspended particles in the water flow through the curved pores in the sand layer, there will be more opportunities and time to collide and contact with the surface of the filter material, so the suspended matter in the water on the surface of the sand layer and the flocculant bond with each other and the contact coagulation process occurs.
Brief summary
To sum up, when we choose the pool sand filter, the larger the filtration area, the lower the filter layer, and the better the filtration effect. The filtration of the swimming pool sand filter is through the process of membrane filtration, osmosis filtration and contact filtration, so that the water can be further purified
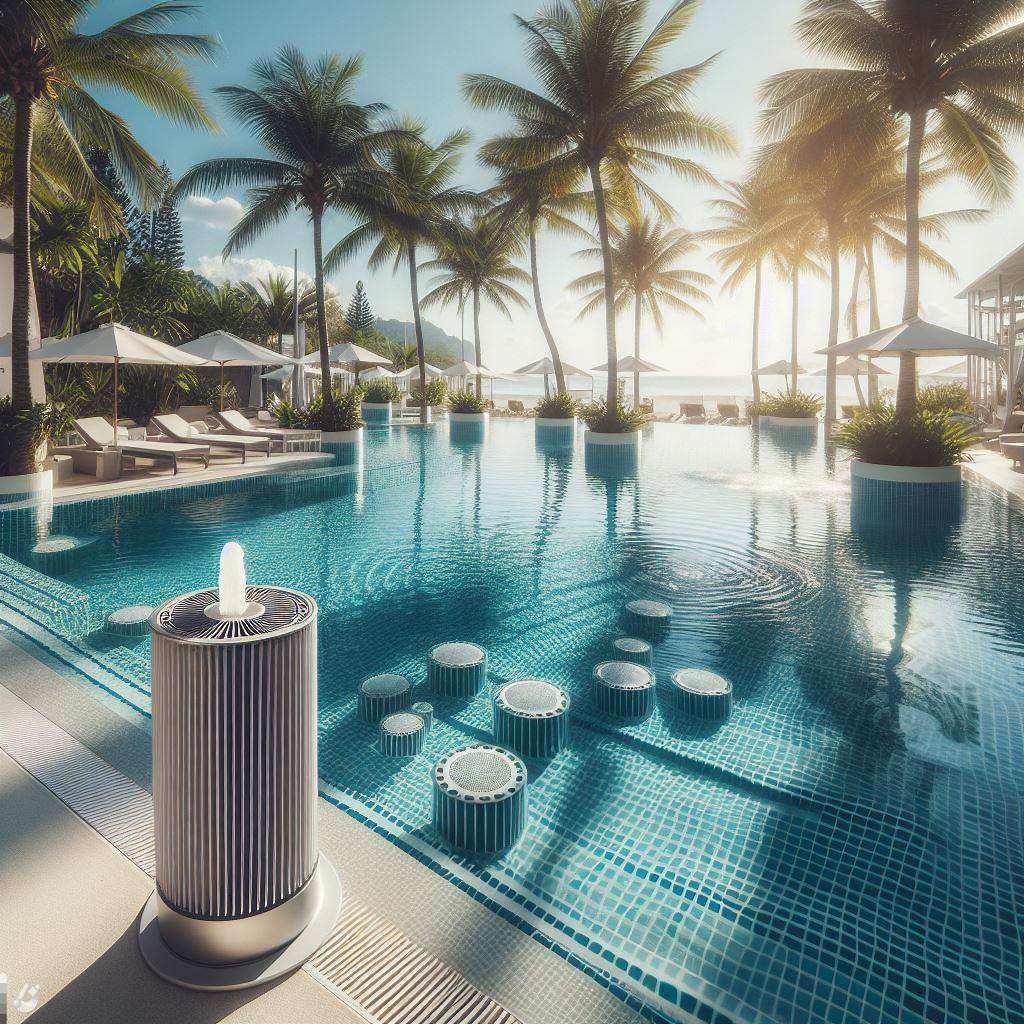
Material classification of pool sand filters
From the material to distinguish, there are three types of common materials of pool sand filters, which are plastic pool sand filters, glass fiber pool sand filters and stainless steel pool sand filters.
Plastic pool sand filter
Plastic quartz sand filter is made of food-grade plastic material. Its advantages include safety, environmental protection, economy, strong corrosion resistance, stronger anti-impact ability, and easy transport.
Glass fiber pool sand filter
The advantages of glass fiber material are strong and durable, not easy to deformation, rupture, wear, chemical corrosion resistance and sunscreen performance, often used in medium and large swimming pool projects.
Stainless steel pool sand filter
Stainless steel pool sand filter is better than glass fiber material performance, but its cost is higher, often used in large swimming pool projects.
Swimming pool sand filter filtration speed
For the competition pool, public pool, special pool, and leisure pool, the sand filter filtration speed ranges from 15 to 25m/h, considered as medium-speed filtration. Excessive filtration speed significantly reduces filtration accuracy, increases filtration resistance, wastes energy, and may lead to filter sand compaction. The number of swimming pool sand filters should be based on factors such as water circulation, water quality, running time, maintenance conditions, etc. Each swimming pool should have at least 2 sets of filters and should be designed for 24-hour continuous operation.